From The Leader in Clean Power Production Technologies
Fort Martin Case Study
Fort Martin Units 1 and 2
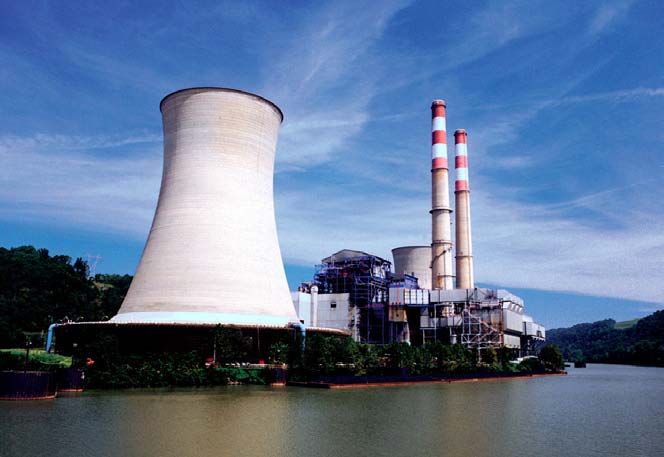
Monongahela Power
Maidsville, West Virginia
Plant Owner
Monongahela Power a subsidiary of FirstEnergy Corp.
Plant Name
Fort Martin Units 1 and 2
Location
Maidsville, West Virginia
Contract Order: 2006
Commercial Operation: 2009
Overview
The wet flue gas desulfurization (FGD) system from Babcock & Wilcox (B&W) features a combination of design components to provide a high level of reliability and removal efficiencies. These include B&W's signature dual tray tower design that provides excellent gas-to-liquid contact and uniform flow distribution through the absorber spray zones; its patented inlet awning; interspatial headers to reduce absorber height, pump power requirements, and internal support costs; forced oxidation system; and advanced mist eliminators.
Boiler/Plant Information
- 2 x 550 MW
- Boiler type: Pulverized coal
- Design fuel: Bituminous
- Additional environmental equipment: Electrostatic precipitator (ESP)
Project Summary
- Engineering, procurement and construction of a wet FGD system
- System designed to remove 98% of the entering sulfur dioxide (SO2)
- Type: Limestone forced oxidation with gypsum byproduct
- Project awarded: April 2006
- Construction plan included on-site scrubber module fabrication area
- Operation dates: November 2009 (Unit 1); December 2009 (Unit 2)
B&W Scope
- Two wet FGD absorbers (one per boiler)
- Two limestone milling systems (one per boiler)
- Gypsum dewatering system including three horizontal table filters (two operating, one spare)
- Buildings and structural steel
- Construction of B&W supplied equipment and steel provided by Babcock & Wilcox Construction Co., Inc.
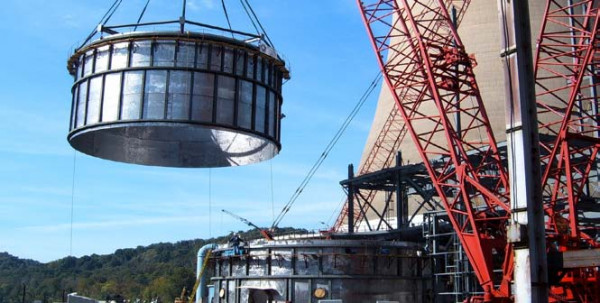
The construction plan included an on-site scrubber module fabrication area that produced absorber modules for both the Fort Martin and Hatfield’s Ferry sites. This plan optimized modularization opportunities because off-site modularization was not feasible due to access constraints created by locks on the adjacent Monongahela River.
Results
Both of the commissioned units have met performance guarantees and achieved mechanical and substantial completion milestones ahead of schedule. Units 1 and 2 started up on schedule one month apart.