The B&W Learning Center
Leading the world in clean power production technology
Boiler Operations Part 2
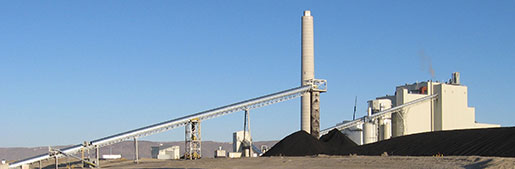
Boiler Operations That Affect Efficiency (Part 2)
In its simplest form, efficiency is the ratio of energy output to energy input, expressed as a percentage. To optimize efficiency, therefore, it is important to minimize input (fuel being a major source) and maximize output (steam production). However, these two goals often have opposing outcomes. This two-part article reviews the operator’s responsibility to effectively manage various techniques and key functions which will optimize efficiency, regardless of fuel or boiler type.
Part 2: Key operation functions
Burner adjustments
The fuel and combustion air combine and release heat at the burners. To maintain optimium heat distribution across the width of the furnace, air and fuel flows must be evenly supplied to all burners. While individual burner adjustments affect a particular burner, they can also impact adjacent burners. Most boilers have multiple burners in parallel flow paths on the front and/or rear furnace walls. Burners must be similar in design and must be adjusted in the same way to optimize air flow distribution.
Adjustments can typically vary the turbulence and flow rates in burners. Increased turbulence increases the air-fuel mixing. It also increases the combustion intensity, provides faster heat release, reduces unburned carbon (UBC) in the ash, permits operation with less excess air, and increases boiler efficiency. However, increased slagging, increased NOx emissions and higher fan power consumption can also result.
Fuel flow adjustments to individual burners are also possible, either through diverter mechanisms in the fuel preparation system or through flow balancing devices in the coal transport piping. While possible, the dynamic balancing of fuel flow is difficult. As with combustion air adjustments, potential impacts to adjacent burners will require reliable feedback on relative flow rates to be effective as a dynamic operational tool. Advances in flame characterization systems and sensors for post-combustion constituents can provide more precise feedback for online fuel balancing. In situ coal and combustion air flow measurement devices are also being used for real-time air and fuel flow measurement. One tool available to operators is the Flame Doctor® flame monitoring system. The system can be attached to any wall-fired unit to monitor the flame quality of each individual burner in comparison to all of the burners. With this information the operator can adjust individual burner air and fuel flows to balance the entire system, improve combustion efficiency, lower excess air, and lower NOx emissions from the furnace.
Fuel flow adjustments to individual burners are also possible, either through diverter mechanisms in the fuel preparation system or through flow balancing devices in the coal transport piping.
Overfire (staged) air port adjustments
Burner systems intended for NOx reduction are typically staged so that the primary combustion elevation is usually operated with less than the theoretical air required for complete combustion. The remaining air needed to complete the burning process is introduced separately, above the highest burner zone, through OFA ports. The staging air flow is typically varied as a function of load, based on parametric testing performed during commissioning. This staging of air to complete combustion of the volatilized fixed carbon and CO gas above the burner zone allows for significant reduction of NOx formation in the reducing atmosphere of the burner zone. While normally satisfactory for ensuring complete combustion and emissions compliance, any changes to fuel type, fuel preparation quality, or the fuel and air transport systems will require close monitoring of OFA system performance.
Excess air
The total combustion air flow to a balanced draft boiler is generally controlled by adjusting the quantity of air from the forced draft fan and controlling the furnace draft with the induced draft fan in relation to the fuel flow. Excess air is the additional combustion air above the amount required to theoretically burn (stoichiometric air) a given amount of fuel. Excess air compensates for mixing inadequacies in the furnace. The benefits of increasing excess air include increased combustion intensity, reduced carbon loss and/or CO formation, and reduced slagging conditions. Disadvantages include increased fan power consumption, increased heat loss up the stack, increased tube erosion, and possibly increased NOx formation.
For most coal ashes, particularly those from eastern U.S. bituminous coals, the solid-to-liquid phase changes occur at lower temperatures if free oxygen is not present (reducing conditions) around the ash particles. As a result, more slagging occurs in a boiler operating with insufficient excess air where localized reducing conditions can occur.
Localized tube metal wastage may also occur in furnace walls under low excess air conditions, but the impact is less clearly defined. The absence of free oxygen (a reducing atmosphere) and the presence of sulfur (from the fuel) are known causes of tube metal wastage. High chlorine levels can also promote tube wastage. Although most coals and conventional fuels contain very little chlorine, it is a severe problem in refuse-derived fuels.
Fuel conditions
Fuel conditions can significantly impact combustion performance of all types of boilers. Fuel conditions include temperature, pressure and particle size. Cooler temperatures, lower pressure and larger particle size contribute to less complete combustion and increased unburned carbon in the ash. Conversely, if the fuel is hotter and finer, combustion is improved. However, NOx emissions and slagging can also increase with these conditions.
Fuel conditions can significantly impact combustion performance of all types of boilers.
Effects of fuel preparation equipment on boiler performance
Fuel preparation equipment readies the fuel for combustion and can have a significant impact on emissions. The preparation equipment includes the crushers, pulverizers and drying systems on coal-fired units; fuel oil heaters and pumps on oil-fired units; refuse handling, mixing or drying equipment on refuse-fired boilers; or fuel handling, blending, sizing and delivery equipment on stoker-fired units. If this equipment is not properly maintained and operated, the fuel may not be completely burned, leaving UBC in the ash or CO in the flue gas.
The operator must monitor the fuel preparation equipment. Knowledge of the equipment, its maintenance record and operating characteristics is essential.
Burning different fuels
The fuel feed system and the grate design for stoker-fired units are based on specific fuel type and sizing of the coal, wood, bark, refuse or other type of solid fuel. If proper sizing is not maintained per the specified design, then operating difficulties and inefficiencies are likely to occur.
The fuel preparation, sizing, delivery and combustion equipment on pulverized coal units are designed to handle a specific type of coal or similar coals if more than one is used. The furnace volume and surface are designed to cool the flue gas below the initial deformation temperature of the ash for the specified design coal. If the coal characteristics vary significantly from the design specifications, then the furnace will be under or over absorbing. This will lead to greater slagging in under-absorbing conditions and less steam generation in the furnace. Over-absorbing conditions result in less heat available in the convection pass for superheating. This will require operator or design changes to achieve desired final steam conditions.
The majority of natural gas- or waste gas-fired boilers are in industrial power plants and heating stations. Most of the package boilers used for heating, cooling and process steam are now fired by natural gas. It is extremely important that operators are knowledgeable on all safety conditions and procedures for operating these units.
Fuel switching coal-fired boilers to natural gas firing because of favorable fuel prices presents other unique challenges. On utility and larger industrial units with superheaters, this may require physical changes to heat traps as well as changes to the burner and fuel handling equipment.
Feedwater and boiler water conditioning requirements
The main function of a boiler is to transfer heat from combustion gases through tube walls to heat water and produce steam. Clean metal tubes are good conductors, but impurities in the water can collect on the inside surface of the tubes. These deposits reduce heat transfer, elevate tube temperatures, and can lead to tube failures. Water conditioning is essential to minimize deposits and maintain unit availability.
Tube deposits reduce heat transfer, elevate tube temperatures, and can lead to tube failures.
Sootblower operations
A sootblower is an automated device that uses steam, compressed air, or high-pressure water to remove ash deposits from tube surfaces. Sootblowing improves heat transfer by reducing fouling and plugging. However, excessive sootblowing can result in increased operating cost, tube erosion and increased sootblower maintenance. Conversely, infrequent sootblower operation can reduce boiler efficiency and capacity. Optimum sootblowing depends on load conditions, combustion quality and fuel. Cleanliness of the heat transfer surfaces has traditionally been left to the operator’s discretion and experience.
However, advanced sootblowing control systems are being deployed to assist operators in providing optimal sootblowing performance. These intelligent sootblowing systems rely primarily on monitoring boiler heat transfer performance to determine the frequency of sootblower operation. Since cleaning is performed based solely on an as-needed basis, the intelligent sootblowing systems are ideally suited for operations dealing with changing fuel blends. Furnace-based sootblowing equipment is increasingly being controlled with advanced control schemes that monitor the heat flux in select zones, supervise blower operation for effectiveness, and minimize thermal shock to the furnace wall tubes.