From The Leader in Clean Power Production Technologies
Hatfield’s Ferry Station Case Study
Hatfield’s Ferry Station Units 1, 2 and 3
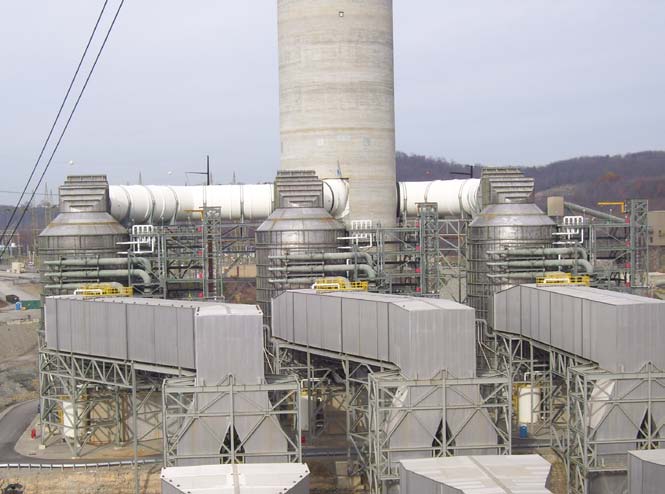
FirstEnergy Generation Corp.
Masontown, Pennsylvania
Plant Owner
FirstEnergy Generation Corp. a subsidiary of FirstEnergy Corp.
Plant Name
Hatfield’s Ferry Station Units 1, 2 and 3
Location
Masontown, Pennsylvania
Contract Order: 2006
Commercial Operation: 2009
The wet flue gas desulfurization (FGD) system from Babcock & Wilcox (B&W) features a combination of design components to provide a high level of reliability and removal efficiencies. These include B&W's signature dual tray tower design that provides excellent gas-to-liquid contact and uniform flow distribution through the absorber spray zones; its patented inlet awning; interspatial headers to reduce absorber height, pump power requirements, and internal support costs; forced oxidation system; and advanced mist eliminators.
Boiler/Plant Information
- 3 x 570 MW
- Boiler type: Pulverized coal
- Design fuel: Bituminous
- Additional environmental equipment: Electrostatic precipitators (ESP)
Project Summary
- Engineering, procurement and construction of a wet FGD system
- System designed to remove 98% of the entering sulfur dioxide (SO2)
- Type: Limestone forced oxidation with gypsum byproduct
- Project awarded: April 2006
- Construction plan included on-site scrubber module fabrication area
- Operation dates:June 2009(Unit 1); October 2009(Units 2 and 3)
B&W Scope
- Three wet FGD absorbers (one per boiler)
- Three limestone milling systems (one per boiler)
- Gypsum dewatering system including four horizontal table filters (three operating, one spare)
- Buildings and structural steel
- Construction of B&W supplied equipment and steel provided by Babcock & Wilcox Construction Co., Inc.
Results
- Achieved mechanical and substantial completion milestones ahead of schedule
- All commissioned units have met performance guarantees
Construction Plan Constraints
The construction plan included an on-site scrubber module fabrication area that produced absorber modules for both the Fort Martin and Hatfield’s Ferry sites. This plan optimized modularization opportunities because off-site modularization was not feasible due to access constraints created by locks on the adjacent Monongahela River.