From The Leader in Clean Power Production Technologies
Open-Bottom Bubbling Fluidized-Bed Technology Case Study
B&W’s Open-Bottom Bubbling Fluidized-Bed Technology Designed for Biomass Firing
Biomass unit meets and exceeds all owner and operator expectations
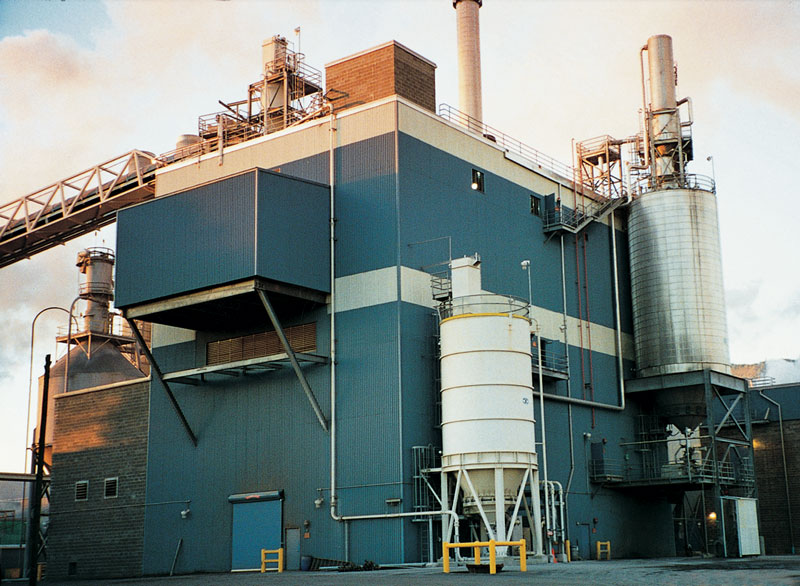
Background
- Mill owners in Oregon approached The Babcock & Wilcox Company (B&W) with multiple goals:
- Burn low cost, mill-generated biomass (bark)
- Dispose of 100% of the mill’s sludge, landfilled at the time
- Produce additional steam that could be fed into the existing plant steam system
- Use steam to generate electricity
- Meet all strict emissions requirements mandated by the Oregon Department of Environmental Quality
Fluidized-bed combustion has been successfully applied to a range of wood and biomass fuels and offers a number of features that may be advantageous in specific applications.
Solution
Bubbling fluidized-bed (BFB) systems are attractive when wide fuel flexibility is required, and for firing high moisture and lower heating value fuels. B&W’s solution – an open-bottom bubbling fluidized-bed unit, was the first such B&W design in North America.
The unit features an open-bottom design to eliminate concerns about rocks and other debris typically found in bark and woody biomass. Non-combustible material is easily removed from the furnace with the boiler in operation. Bed temperature is controlled to limit nitrogen oxides (NOX) emissions and to limit bed material agglomeration. The controlled burning within the bubbling bed helps control the combustion temperature, providing better control of emissions levels over a range of changing fuel conditions. Also, a flue gas recirculation system allows operation of the boiler over an even wider range of fuel moistures.
The unit is now burning all of the mill’s sludge and is operating successfully at 25% above the original rated capacity. In addition, the sludge is supplemented with low-grade, high-moisture bark, in plentiful supply at the mill.
Additional Benefits
- To reduce construction time and impact on other mill operations, the boiler was ground-assembled in two major sub-assemblies, then lifted into place on successive days. The mill continued to run at full capacity throughout boiler installation.
- The additional steam has allowed the mill to reduce its former reliance on a natural-gas-fired unit, thereby greatly reducing fuel costs, and fuel price uncertainty.
- No emissions scrubber was required on this unit, due to its low-emissions design.
- Landfill cost of sludge disposal was virtually eliminated.