From The Leader in Clean Power Production Technologies
Wood-fired Combined Heat and Power Plant
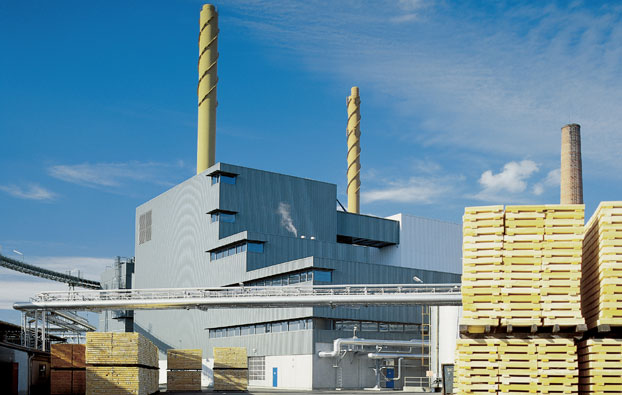
Junckers Industrier A/S is Denmark’s largest wood processor and manufacturer. The factory processes more than 500,000 tons of logs into solid wood parquet flooring and tabletops annually. In July 1996, Junckers Industrier A/S contracted with Babcock & Wilcox Vølund A/S (B&W Vølund) for the building of a new multifuel-fired combined heat and power (CHP) plant.
The plant was delivered as a turnkey supply and commissioned in April 1998. The wood which is found unsuitable for flooring and tabletops is used in the manufacture of medium-density fibreboard (MDF) plates. A portion is used as fuel in Juncker’s own combined heat and power (CHP) plant which supplies the factory with power.
B&W Vølund’s natural circulation boiler fires waste wood (mainly consisting of sawdust, shavings, slip and wood chips) as well as oil and biogas.
The combustion equipment for the different fuels consists of:
• Two dust burners, placed at different levels at each side of the furnace side walls, intended for fine-grained fuel. Oil burners for emergency and support firing are integrated in the dust burners.
• Three pneumatic air spouts for the coarse fuels installed on the boiler front. At the bottom of the furnace, a water-cooled vibrating grate is arranged to ensure combustion of the coarse fuel which does not have sufficient time to burn out while passing through the furnace in suspension.
Secondary combustion air and recycled flue gas are supplied to the furnace combustion zone through nozzles in the boiler front and rear walls. Slag and ash are transported to containers by means of a submerged slag conveyor system.
The flue gases leave the boiler and are carried through an electrostatic precipitator which removes the fly ash from the flue gases before they are carried up through the 70 m-high steel chimney